В связи с этим процессы выделения карбидной фазы (цементита) происходят в период охлаждения при закалке. Поэтому в рассматриваемых сталях первое превращение при отпуске практически отсутствует. Действительно, авторы работы отмечают, что в результате первой стадии распада мартенсита после отпуска при 100-150° С содержание углерода в нем понижается от 1,2 до 0,2-0,25 %. Такая микроструктура получила название отпущенного мартенсита. У малоуглеродистых низколегированных сталей такая микроструктура формируется непосредственно после охлаждения в воде.
По данным работы предел прочности закаленных в воде сталей 14Х2ГМР и 14ХМНДФР практически не изменяется после отпуска при температурах ниже 150° С и составляет 1350-1400 Н/мм2.
В этих сталях после охлаждения в воде имеется определенное количество остаточного аустенита (~5 %). Поэтому при отпуске протекает второе превращение — распад остаточного аустенита. После отпуска стали 14Х2ГМР при температуре 450° С структура состоит из цементита и остаточного аустенита, т.е. аналогична структуре закаленной стали. Начиная с отпуска при температуре 550° С, на рентгенограмме фиксируется только цементит. Это показывает, что остаточный аустенит полностью распадается по механизму промежуточного превращения.
После отпуска при 650° С плотность дислокаций в результате протекания процессов полигонизации и аннигиляции резко снижается. Можно наблюдать первые стадии рекристаллизации ферритных реек. При дальнейшем повышении температуры отпуска происходит интенсивная трансформация структуры закалки вследствие более полного протекания процессов полигонизации и рекристаллизации ферритной матрицы. Рейки уступают место равноосным ферритным зернам разных размеров, что является следствием неравномерности рекристаллизации на различных локальных участках. Такие изменения микроструктуры приводят к значительному разупрочнению сталей.
У стали 15ХГ2СМФР при температурах отпуска 500-550° С прочностные свойства несколько увеличиваются. Это связано с выпадением специальной карбидной фазы. Зарождение карбидных частиц может происходить у различных дефектов кристаллического строения, что зависит как от пересыщения твердого раствора по компонентам, так и от плотности данного типа дефектов кристаллического строения. Наличие в мартенсите высокой плотности дислокаций значительно расширяет температурную область зарождения дисперсных частиц. При отпуске мартенсита в условиях легкого зарождения и высокой диффузионной подвижности атомов наблюдается высокая скорость выделения карбида — в четыре раза выше, чем в бейните.
Первые выделения карбида ванадия наблюдаются после отпуска при 500° С. Легкое зарождение карбидов при отпуске мартенсита приводит к образованию частиц, многочисленных и весьма разнообразных по размеру и составу (по данным анализа экстракционных угольных реплик). Кроме цементита Fe3C и карбида ванадия VC, в этой стали имеются карбид хрома Сr7С3 и карбид молибдена (Fe, Мо)23С6.
После выделения из матрицы стали специальных карбидов наступает стадия коагуляции карбидной фазы, чему способствует повышение температуры отпуска до 600° С и выше. По данным работы, карбидные фазы по склонности к коагуляции частиц при отпуске можно расположить в следующей последовательности, начиная с меньшей: Fe3C, Ме3С, Ме7С3, Ме2С, VC, NbC, TiC. В рассматриваемых сталях формирование рациональной субструктуры начинается при более высоких температурах отпуска, при которых заканчивается выделение специальной карбидной фазы: при 620-650° С, а в некоторых случаях при 680-700° С. Лишь начиная с этих температур отпуска, происходит резкое увеличение ударной вязкости.
Таким образом, температура отпуска сталей с мартенситной структурой зависит от их химического состава и должна обеспечивать рациональное соотношение полигонизованных и рекристаллизованных структурных составляющих, что обеспечит оптимальное соотношение прочности стали и ее максимально возможное сопротивление хрупким разрушениям.
Стали с мартенситной структурой
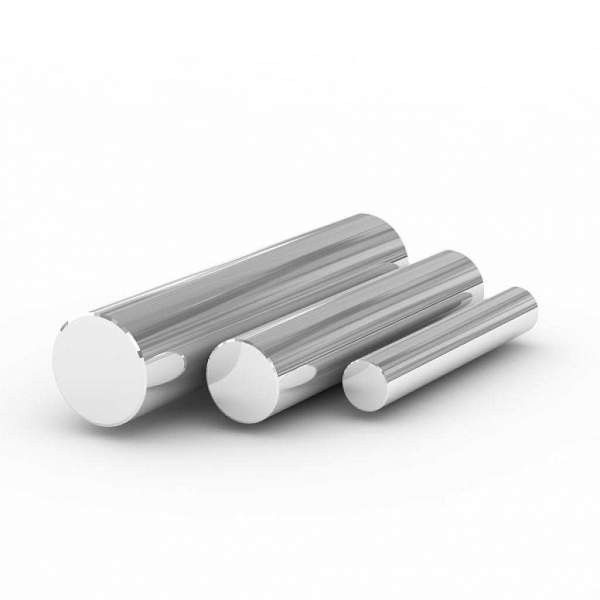
- 05/12/2013
- 2777 views
При описании мартенситной структуры отмечалось, что температура начала мартенситного превращения малоуглеродистых низколегированных сталей составляет ~400° С.