К стали, разливаемой на УН PC, предъявляют жесткие требования по температуре и жидкотекучести. Эффективным средством повышения жидкотекучести является раскисление стали силикокальцием (3-4 кг/т), при этом количество алюминия может быть снижено до 0,3-0,4 кг/т. Температура стали перед разливкой на УНРС должна быть на 30-40° С выше, чем при обычной разливке. Этот перегрев может быть снижен при предварительном нагреве сталеразливочных ковшей до 600-800° С, а промежуточных до 1000° С.
Сталь в кристаллизатор должна поступать равномерно хорошо сформированной струей. Для обеспечения устойчивого процесса разливки и получения удовлетворительной поверхности слитков (заготовок) необходима равномерная подача на стенки кристаллизатора смазки, одновременно с которой подается пропан-бутановая газовая смесь.
Для получения оптимальной структуры и плотной осевой зоны непрерывнолитой заготовки должны быть оптимизированы следующие технологические параметры: температура и скорость разливки, а также интенсивность вторичного охлаждения.
Раскисление и легирование кислородно-конвертерной низколегированной стали для непрерывной разливки предпочтительней вести жидким ферромарганцем и твердым силикомарганцем, присаживаемыми в ковш перед началом разливки. По мере освоения технологии производства стали для газопроводных труб на УН PC брак листа по дефектам поверхности и брак заготовок значительно уменьшились. В частности, были преодолены затруднения, связанные с ухудшением поверхности заготовок и листов при повышенной добавке алюминия. Необходимость такого повышения вызвана стремлением получить в листах достаточно высокую ударную вязкость при температуре испытаний —40° С. B.C. Рутес, П. Н.Ткачев и др. показали, что выбор оптимальной схемы раскисления, подвод стали в кристаллизатор с помощью удлиненных стаканов под уровень мениска и использование защитных покрытий дают возможность в случае необходимости повысить расход алюминия до 1,0-1,5 кг/т. Это было подтверждено практикой работы ряда отечественных заводов.
В настоящее время около 50 % выплавляемой в мире стали разливают на машинах непрерывного литья заготовок. В промышленно развитых странах на МНЛЗ разливают до 90% производимой стали. В Италии, США, Германии и Японии практически вся сталь массового назначения разливается на МНЛЗ.
Несмотря на сложность и высокую стоимость МНЛЗ, из-за неоспоримых преимуществ, основными из которых являются высокая производительность и стабильность процесса, повышенный выход годного, высокое качество металла, возможность автоматизации процесса, а также отличная вписываемость в единый технологический цикл от сталеплавильного агрегата до получения готовой продукции, непрерывная разливка стали в нашей стране постоянно расширяется.
Специфические условия эксплуатации МНЛЗ, а также необходимость получения непрерывнолитых заготовок высокого качества требуют иных подходов к производству стали.
Кратко, с позиций металловедения рассмотрим напряжения, возникающие в затвердевающей корочке и приводящие к образованию трещин в непрерывнолитых заготовках, механические свойства последних.
Механические напряжения, возникающие от усилий вытягивания и трения заготовки о стенки кристаллизатора, ферростатического давления на корочку застывающей стали, искривления заготовки и ее Деформации часто Являются причинами образования внутренних и поверхностных трещин, которые в дальнейшем могут привести к возникновению дефектов в прокате и готовых изделиях. Схема расположения типичных трещин, которые могут возникнуть в процессе кристаллизации и затвердевания непрерывнолитой заготовки. От сил трения растягивающие напряжения возникают в заготовке, если кристаллизатор перемещается вверх относительно заготовки. Температурный градиент в затвердевающей корочке вызывает снаружи растягивающие напряжения, а на фронте кристаллизации — сжимающие. При изменении условий охлаждения в зоне вторичного охлаждения возможно локальное увеличение температуры поверхности заготовки, что приводит к изменению напряженного состояния в поверхностном слое и на фронте кристаллизации.
Ферростатическое давление столба жидкого металла в центральных слоях оказывает двоякое воздействие на отвердевшую поверхность заготовки. Во-первых, оно препятствует температурной усадке корочки и вызывает тем самым возникновение круговых растягивающих напряжений. Во-вторых, из-за растяжения корочки устраняется зазор между заготовкой и кристаллизатором, что приводит к возникновению термических напряжений из-за более быстрого охлаждения, а также к возрастанию силы тренгя. Ниже уровня кристаллизатора ферростатическое давление вызывает раздутие заготовки между роликами. При этом возникают растягивающие напряжения в наружном слое корочки и сжимающие напряжения на фронте кристаллизации. Дополнительно из-за разбухания заготовки между валками и сжатия ее на валках происходит перетекание жидкой сердцевины, что усиливает ликвационные процессы.
Вес заготовки и усилия от ее вытягивания приводят к появлению продольных растягивающих напряжений. От изгиба и выпрямления заготовки возникают растягивающие или сжимающие напряжения.
Дополнительными причинами возникновения напряжений могут быть конструктивные или технологические неполадки, а также нарушения параметров эксплуатации МНЛЗ; наиболее распространенными из них являются эксцентричное расположение роликов, увеличенные зазоры между роликами, появляющиеся, в частности, из-за износа последних, плохая наладка машины и др.
Результаты расчетов и экспериментов показывают, что растягивающие напряжения в корке и в более глубоких слоях заготовки переходят в сжимающие. Кроме того, установлено, что существуют интервалы температур пониженной прочности и пластичности заготовки в процессе ее кристаллизации. При температурах от солидус до 1340° С появляется большинство трещин всех разновидностей. Низкая прочность затвердевающего металла объясняется присутствием в междендритных областях жидких прослоек, обогащенных фосфором и серой. При этом фосфор в большей степени снижает прочность затвердевающего металла, чем сера. Вредное влияние серы в этой температурной области устраняется повышенной концентрацией марганца. Повышенные концентрации углерода не влияют отрицательно на прочностные характеристики заготовки.
В интервале температур 1200-800° С сталь имеет низкую пластичность и плохо сопротивляется деформациям. Деформируемость стали в этой температурной области в сильной степени зависит от содержания марганца и серы, а также от отношения Mn/S. С повышением этого отношения пластичность возрастает. Пониженная пластичность объясняется выделениями сульфидов в форме пластин (плен), снижающих сцепление между зернами.
Все внутренние трещины, располагающиеся в поперечном сечении непрерывнолитой заготовки (трещины типов 1-6) возникают при высоких температурах (от солидус до 1340° С). Трещины типа 1 возникают из-за наличия пленки при высоких температурах металла. Эти трещины являются следствием слишком интенсивного вторичного охлаждения и высокой температуры разливки и четко выявляются на серных отпечатках. Склонность стали, содержащей 0,17-0,25% С, к трещино-образованию повышается при увеличении содержания фосфора и серы, при концентрациях Мn, Сr, Ni более 1 % каждого, более 0,5 % Si, а также при наличии в стали алюминия. Склонность к трещинообразованию уменьшается при содержаниях углерода и кремния менее 0,16% и 0,50% соответственно, марганца более 0,25 %.
Причиной образования трещин типа 2 является раздутие широкой грани заготовки из-за недостаточной толщины корочки. Раздутие заготовки ведет к возникновению на узкой грани заготовки растягивающих напряжений, которые достигают максимальных значении на фронте кристаллизации. Предотвратить образование этих трещин можно только точным и плавным перемещением заготовки.
Трещины типа 3 тоже могут возникать из-за раздутия заготовки по широкой грани на нижних горизонтах МНЛЗ, где ферростатическое давление в заготовках достаточно велико. Их образование можно предотвратить правильным размещением тянущих роликов и низкой скоростью разливки, а также интенсивным вторичным охлаждением.
Трещины типа 4 возникают, как правило, в квадратных заготовках при искажении сечения (ромбичности) и размещаются вдоль короткой диагонали
Трещины типа 5 возникают при деформации заготовки (изгибе или выпрямлении) с жидкой сердцевиной или заготовки, полностью затвердевшей, но имеющей в центральных слоях температуру выше 1340° С.
Трещины типа 6 возникают при большом сжатии заготовки тянущими роликами, если сердцевина еще жидкая или температура ее превышает 1340°С.
Трещины типа 7 возникают из-за неравномерности охлаждения металла в кристаллизаторе и располагаются на поверхности широкой грани. При правильном выборе параметров разливки они короткие и неглубокие и легко удаляются при огневой зачистке.
Трещины типа 8 возникают, как правило, на квадратных заготовках при искажении профиля (ромбичности), а также при повышенном содержании в стали серы и фосфора (> 0,035 % каждого).
Возникновение трещин типов 9 и 10 в значительной степени зависит от содержания в стали марганца (более 1 %) и модифицирующих добавок (кроме титана). Трещины этих типов проходят по границе аустенитных зерен по местам скопления нитридов, карбидов и карбонитридов.
Возникновение трещин типа 11 (паукообразных и сетчатых) зависит от параметров вторичного охлаждения и материала, находящегося между корочкой заготовки (медь, шлаковые покрытия и др.) и кристаллизатором.
Как следует из вышеизложенного, в промежуточном ковше МНЛЗ в той или иной степени могут быть воспроизведены практически все операции и процессы, которые осуществляют при внепечной обработке стали. Поэтому непрерывная разливка стали является одним из составных звеньев ковшовой металлургии, предопределяющей высокое качество проката и изделий из непрерывнолитой стали.
Для внепечной обработки стали на МНЛЗ созданы промежуточные ковши различных конструкции, оборудованные приспособлениями, позволяющими производить операции, значительно улучшающие качество металла: продувку инертными газами, перемешивание, индукционный подогрев, охлаждение, формирование синтетического шлака, поглощение шлаком неметаллических включений и др. Кроме того, применяют различные способы воздействия на кристаллизующийся металл: электромагнитное перемешивание, позволяющее изменять (регулировать) форму растущих дендритов, электромагнитное торможение (EMBR — Electromagnetic Brake) для замедления скорости поступления металла в кристаллизатор и др.
Непрерывная разливка стали
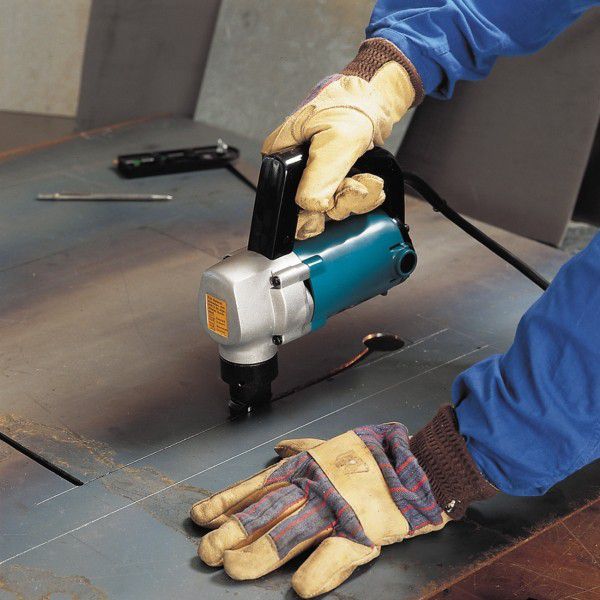
- 05/12/2013
- 5650 views
Для непрерывной разливки в основном применяют установки трех типов: вертикальные, вертикальные с изгибом слитка и радиальные (криволинейные).