Такая обработка получила название деформационно-термическое упрочнение (ДТУ). ДТУ предусматривает снижение температуры конца прокатки в области АГ, деформацию по регламентированному режиму и последующее ускоренное охлаждение с регламентируемой скоростью. В результате такого охлаждения в прокате малоуглеродистых и низколегированных сталей ферритно-перлитного класса формируется более дисперсная феррито-цементитная смесь, чем при упрочнении со специального нагрева. Поэтому прокат приобретает большую прочность и одновременно большее сопротивление хрупким разрушениям. При использовании ДТУ многократно (до 10 раз и более) снижаются расходы топливно-энергетических ресурсов, затраты на капитальное строительство и эксплуатационные расходы, а также значительно уменьшаются потери металла на вторичную окалину.
В настоящее время на металлургических комбинатах России разработаны и освоены процессу ДТУ сталей массового потребления.
Деформационно-термическое упрочнение проката осуществляется с целью максимально полной реализации потенциальных возможностей, обусловленных химическим составом обычных, как правило, стандартных углеродистых и низколегированных сталей, широко применяющихся в строительстве и машиностроении.
Деформационно-термическое упрочнение осуществляется в едином с прокаткой тепловом цикле с использованием тепла прокатного нагрева.
Принципиальное отличие деформационно-термического упрочнения от контролируемой прокатки заключается в отсутствии необходимости жесткого регламентирования температурных, деформационных и энергосиловых параметров, снижающих производительность станов и существенно увеличивающих нагрузки на оборудование при производстве проката. Деформационно-термическое упрочнение может осуществляться на существующих маломощных станах, оснащенных системами для умеренного охлаждения проката после завершения обжатий. Этот процесс является эффективным способом целенаправленного воздействия на структуру малоуглеродистой стали с простой композицией химических элементов, не содержащей дорогих и дефицитных микродобавок, позволяющий формировать заданный комплекс механических и эксплуатационных свойств проката в процессе горячей деформации и последующего ускоренного охлаждения.
Деформационно-термическое упрочнение в потоке толстолистовых, универсальных и непрерывных широкополосных прокатных станов позволяет поднять прочностные характеристики углеродистой стали СтЗсп до уровня низколегированной и обеспечить их равноценную замену. Ударная вязкость при отрицательных температурах, а также пластичность упрочненной углеродистой стали значительно выше, чем у низколегированной стали, равной прочности, что обусловлено высокой степенью дисперсности и мелкозернистости структуры.
Однако производство рулонной стали с высокими механическими свойствами связано с известными трудностями. Прокатка с большими скоростями, очень медленное охлаждение полосы, смотанной в рулон при высоких температурах, приводят к неблагоприятным структурным превращениям в интервале температур наименьшей устойчивости аустенита. При охлаждении в рулоне с очень низкой скоростью в различных температурных интервалах в общем случае реализуются процессы отпуска, сопровождающиеся структурными изменениями, которые из-за недостатка времени не могут осуществиться при тех же температурах в случае охлаждения листов или полос на рольганге. Из-за неравномерного охлаждения полоса имеет различные структуры и механические свойства подлине. Для обеспечения удовлетворительного ее качества металл необходимо легировать элементами, обеспечивающими устойчивость против разупрочнения в этих условиях. Таким элементом является кремний. Однако известно отрицательное влияние кремния при его содержании более 0,5 % на вязкие свойства стали с феррито-перлитной структурой.
Как отмечалось, основным технологическим параметром при производстве упрочненной широкополосной стали на непрерывных станах является скорость охлаждения полосы в интервале температур наименьшей устойчивости аустенита (800-550° С). Уровень и однородность механических свойств определяются также температурой смотки полосы в рулон. В зависимости от требуемых прочностных характеристик и химического состава стали скорость охлаждения полосы выбирается в пределах от 7 до 30° С/с. Охлаждение полосы осуществляется на отводящем рольганге специальными устройствами, позволяющими регулировать давление, расход и скорость подачи воды. Высокая эффективность процесса достигается при охлаждении водо-воздушной смесью с различным, выбираемым в каждом конкретном случае соотношением компонентов.
В результате ускоренного регулируемого охлаждения широких полос после прокатки формируется мелкозернистая феррито-перлитная структура с размерами ферритного зерна 4-10 мкм, обеспечивающая высокие механические и эксплуатационные свойства малоуглеродистой стали.
Регулируя температурно-временные параметры охлаждения после прокатки, можно изменять в широком диапазоне характеристики прочности и вязкости широкополосного проката из стали одного и того же химического состава. Предел текучести может изменяться на 200 Н/мм2, условный порог хладноломкости — на 90° С. Известно, что на вязкие свойства влияет содержание в стали серы и фосфора. Изменяя их содержание, можно получить заданный уровень этих свойств.
Наряд; с интенсивностью охлаждения после прокатки дополнительное повышение прочности и улучшение характеристик вязкости получают, увеличивая степени обжатия на завершающей стадии прокатки. Так, при увеличении степени обжатия с 25 до 40 % в температурном интервале Гк.п + 50° С кривые ударной вязкости и условные пороги хладноломкости смещаются на 20-30° С в сторону отрицательных температур. Прочность при этом увеличивается на 50 Н/мм2.
Для гарантированного обеспечения при производстве на непрерывных широкополосных станах упрочненного проката классов прочности 345 и 390 по ГОСТ 19281-89 (сталь С345 и С390 по ГОСТ 27772-88) из углеродистой типа СтЗ, а также низколегированной стали с пониженным содержанием углерода и марганца микродобавка в металл до 0,006% бора оказывается достаточно эффективной: стабилизируя аустенит, бор понижает температуру его распада. При использовании бора заданные высокие характеристики прочности обеспечиваются при более низких скоростях охлаждения, меньших нагрузках на прокатное оборудование и моталки. Авторами установлено, что аналогичное влияние на свойства проката оказывает также ниобий в количестве до 0,04 %, применение которого более предпочтительно при разливке стали на MHJ13.
Упрочненной в процессе деформационно-термического производства широкополосной рулонной стали и полученным из нее листам свойственна анизотропия ударной вязкости. Это обусловлено доминирующей долей энергии, затрачиваемой на развитие трещины, которая в значительной степени зависит от направления прокатки. Энергия, затрачиваемая на зарождение трещины, практически не зависит от направления деформации.
Металлографические исследования позволили установить роль отдельных составляющих структуры в формировании прочностных свойств такого проката. При помощи статистической обработки методом регрессионного анализа результатов исследований получены количественные зависимости между пределом текучести, размером зерна феррита и долей бейнитной составляющей в структуре. Так, уровень прочности свариваемой строительной стали С285 и С345 (ГОСТ 27772-88), а также классы прочности 295-345 (ГОСТ 119281-89) обеспечиваются только при диаметре ферритных зерен не более 10 и 7 мкм соответственно. Требуемые значения предела текучести можно получить и при более крупном зерне, однако в этом случае структура стали должна быть феррито-бейнитной и содержать 5 % бейнита. При содержании бейнита до 12% не отмечено заметного снижения пластичности и вязкости.
Дополнительно повысить ударную вязкость можно, увеличив содержание алюминия в стали. Исследования показали, что увеличение содержания алюминия до 0,05% повышает на 15-21 Дж/см2 ударную вязкость при отрицательной температуре проката, упрочненного по любой из рассмотренных схем.
Увеличение содержания алюминия сверх указанного количества (0,05 % А1) не приводит к заметному улучшению свойств упрочненной стали. При непрерывной разливке стали с повышенным содержанием алюминия необходима тигельная защита струи для предотвращения окисления.
Регулируя и контролируя температурные и деформационные параметры прокатки и скорость охлаждения листов и полос в температурном интервале наименьшей устойчивости аустенита, получают гарантированные уровни предела текучести: 300-350 Н/мм2 — для свариваемой углеродиетой стали с содержанием углерода не более 0,25 % и 400-500 Н/мм2 — для низколегированной стали, в том числе малоперлитной с содержанием углерода до 0,12%, микролегированной ванадием, титаном, ниобием и другими карбидо- и нитридообразующими элементами. Контроль и изменение-технологических параметров упрочняющей обработки в потоке станов необходимо осуществлять с учетом содержания углерода в стали и толщины проката.
Результаты исследования эффективности деформационно-термической обработки упрочненного листового и рулонного проката из углеродистой стали в потоке непрерывных широкополосных станов 2000 свидетельствуют о высокой рентабельности такой технологии. Производство упрочненного листового проката различных классов прочности с пределом текучести до 345 Н/мм2 (ГОСТ 19281-89) по заданным температурным, деформационным и временным параметром в едином с прокаткой тепловом цикле при невысоких дополнительных затратах обеспечивает его конкурентоспособность на рынке проката массового назначения и дает значительную прибыль.
Анализ и обобщение результатов исследований, выполненных совместно металлургическими предприятиями и ведущими институтами потребляющих отраслей, показали, что листы из углеродистой стали, упрочненные в потоке станов, по механическим и эксплуатационным свойствам полностью соответствуют требованиям, предъявляемым к прокату из низколегированной стали повышенной прочности, и характеризуются высокими показателями сопротивления разрушению и хладостойкостью при низких температурах, а также хорошей обрабатываемостью в холодном состоянии и свариваемостью в широком диапазоне тепловложения, не разупрочняясь в зоне термического влияния.
^Результаты дюрометрического анализа показывают, что поверхность листан несколько прочнее сердцевины из-за малой прокаливаемости малоуглеродистой стали. В поверхностных слоях формируются небольшие остаточные напряжения сжатия, благоприятно влияющие на работоспособность конструкций.
Глубокий металлографический анализ позволил установить, что исследуемый прокат имеет структуру, представляющую собой феррито-цементитную смесь различной морфологии, характерной для металла, упрочненного по технологии контролируемой прокатки с деформацией нерекристаллизованного аустенита, когда процессы отпуска прошли достаточно полно.
Методами оптической металлографии в микроструктуре выявляются характерные ферритные зерна, образовавшиеся на месте аустенитного зерна. Размер ферритных зерен сильно зависит от скорости охлаждения после прокатки. Внутри этих зерен наблюдается субзеренная структура с размером субзерен 3-4 мкм. Внутри таких субзерен, в свою очередь, имеет место тонкая структура по типу полигонизации с размером фрагментов 0,3-0,4 мкм. Такая трехслойная структура и обеспечивает достаточно высокое сопротивление проката разрушению.
Приведенные результаты показывают, что в качестве стали С390 (ГОСТ 27772-88) может использоваться деформационно-термически упрочненная сталь типа 09Г2С или другие экономнолегированные стали, упомянутые выше. Наиболее хладостойким является прокат, упрочненный в потоке стана, из малоуглеродисстой стали с прочностными характеристиками С345 и С375.
Прокатка стали на современных непрерывных широкополосных станах отличается от горячей прокатки на реверсивных станах, в первую очередь, деформацией в чистовых клетях, которая осуществляется непрерывно, практически без пауз.
Прокатку на стане 2000 ЧерМК. производили из слябов сечением 250 х 1500 мм. Для обеспечения требуемого комплекса свойств были разработаны и установлены следующие основные деформационно-температурные параметры: температура начала прокатки — 1200... 1250° С; деформация (обжатие) в трех последних чистовых клетях — 40...50 %; температура конца прокатки — около 800° С; скорость охлаждения водой в процессе и после окончания прокатки с умеренными скоростями в середине сечения полосы толщиной 6 мм — 11...13° С/с, при толщине полосы 8 мм — 8... 10°С/с; температура смотки полосы в рулон — 550-580° С.
Кратко прокомментируем выбранные условия. Температура нагрева слябов при прокатке по упрочняющим режимам (1200-1250° С) несколько ниже, чем при обычной горячей прокатке (1280° С). Однако именно выбранный температурный режим обычно рекомендуется при прокатке по упрочняющим схемам на непрерывных широкополосных станах. Такая достаточно высокая температура нагрева обусловливает хорошую горячую пластичность, в результате чего в черновой группе клетей стана обеспечивается получение подката толщиной 20-40 мм (с первоначальной толщины 250 мм).
При прокатке в черновой группе клетей протекают процессы высокотемпературной деформации стабильного аустенита при быстро идущей рекристаллизации; при этом температура деформации существенно выше температуры рекристаллизации аустенита. При выходе из черновых клетей температура подката составляет 1150-1050° С.
Все это убеждает, что выбранные режимы деформации в трех последних чистовых клетях в 40-50% близки к оптимальным. Ускоренное охлаждение в диапазоне 800-580° С, т. е. в диапазоне превращения, которому подвергается полоса за последней клетью перед смоткой, предотвращает рекристаллизацию аустенита и усиливает измельчение зерна, в этом случае можно обойтись без добавок сильных карбидообразующих элементов (ниобия и др.), которые измельчают структуру, задерживая рекристаллизацию аустенита, в отличие от схемы прокатки полосы на реверсивных листовых станах. Стан 2000 оборудован мощной системой охлаждения ламинарными потоками воды с расходом до 15 000 м3/ч, что позволяет охлаждать листы перед смоткой в рулон с требуемой скоростью в 10-20° С/с. Важную функцию имеет межклетевое охлаждение подката водой, позволяющее сохранить высокую производительность стана.
В целом рассмотренную схему прокатки с упрочняющей обработкой можно условно классифицировать как ВТМО с регулируемым ускоренным охлаждением с деформацией нерекристаллизованного аустенита.
Надо заметить, что упрочненные таким образом листы не будут обладать требуемым уровнем сопротивления хрупким разрушениям без последующего отпуска. Отпуск полос проходит при медленном охлаждении рулонов; температурой смотки в рулон регулируется требуемая степень отпуска. При обычной прокатке температура смотки составляет около 700° С. Понижение температуры смотки до принятых 550-620° С приводит к образованию более дисперсной структуры. Отпуск листов и полос (универсальные станы), ускоренно охлажденных после завершения деформаций до температуры ~600° С, осуществляется за счет тепла, аккумулированного во внутренних слоях проката, охлаждение которого следует производить в стопах.
Микроструктурный анализ деформационно-термически упрочненной стали подтвердил, что описанный выше процесс реализуется при упрочнении проката с достаточной полнотой.
Рассмотренная технологическая схема деформационно-термического упрочнения позволяет получить прокат с ат = 345...375 Н/мм2 в сочетании с высокой хладостойкостью из микролегированной малоуглеродистой стали типа 18САТЮ при режимах, близких к обычной горячей прокатке.
Описанный процесс имеет место при прокатке широкополочных двутавровых балок с полками толщиной до 15-20 мм на универсальном балочном стане УБС1300 НТМК при температурах конца прокатки 850-880°С.
Рассмотрим некоторые примеры упрочнения в потоке станов по схеме ДТУ микролегированной малоуглеродистой стали.
В сталях, микролегированных титаном и ванадием, титан предотвращает статическую рекристаллизацию аустенита и тем самым измельчает зерно. Добавки ванадия при подобной технологии измельчают зерно и снижают максимальную твердость в зоне термического влияния сварки.
Для дальнейшего упрочнения проката из рассматриваемых сталей разработаны схемы упрочнения, предусматривающие целенаправленное формирование в готовом прокате дисперсных феррито-цементитных структур с повышенной концентрацией нитридной (карбонитридной) фазы и организованным распределением дефектов кристаллического строения. Такие схемы предусматривают реализацию фазовых превращений в процессе термической обработки или комбинацию горячей пластической деформации и фазовых превращений в различной последовательности
При исследовании плавки 1 оказалось, что прочность сталей со структурой вырожденного перлита даже выше, чем у улучшенной стали. Пластичность также сохраняется на высоком уровне.
Металлографические исследования показали, что микроструктура горячекатаного металла состоит не только из феррита (с размером зерна 8 балла) и пластинчатого перлита, доля которого в структуре составляет 10 %, но и видманштетта, верхнего бейнита и мартенсита, общая доля сдвиговых структур составила 20 %. После высокотемпературного отпуска сдвиговые структуры превратились в мелкие (0,1-0,3 мкм) зерна и субзерна и глобулярные частицы цементита размером 0,05-0,10 мкм.
Проведенные сопоставления структуры и механических свойств проката после горячей деформации и дополнительного высокотемпературного отпуска показали, что наличие большого количества сдвиговых структур является главной причиной низких вязкости и хладостой кости металла.
Исследовали влияние видманштеттовой структуры на механические свойства полуспокойных и спокойных сталей СтЗпс, СтЗсп, 16Г2АФ, 18Г2АФпс. Рост аустенитного зерна при повышении температуры нормализации наблюдали с помощью вакуумного высокотемпературного микроскопа.
Приведенные результаты показывают, что сдвиговые структуры приводят к понижению механических свойств, прежде всего хладостой кости проката с феррито-перлитной структурой. Эффективным способом подавления формирования сдвиговых структур является микролегирование сталей в процессе их производства.
Из сравнения сталей СтЗпс и СтЗсп, 18Г2АФпс и 16Г2АФ и, особенно, типа 10Г2С и ЮГСМЮ видно, что присутствие дисперсных частиц нитридов алюминия в структуре сталей СтЗпс, 16Г2АФ и, особенно стали ЮГСМЮ, существенно улучшает механические свойства проката как прочностные так и, в первую очередь, сопротивление хрупким разрушениям.
Дисперсная фаза (A1N) способствует измельчению аустенитного и ферритного зерна и устраняет структуры сдвигового типа в феррито-перлитных сталях. Это подтверждается тем, что во всех рассматриваемых случаях опасность перегрева сильнее в сталях, не содержащих эффективных количеств дисперсной фазы (A1N). В частности, после нагрева до 900 и 950° С в стали ЮГСМЮ сдвиговые структуры фактически отсутствуют, а в стали 10Г2С их больше 5 %.
Частицы A1N в стали ЮГСМЮ сохраняются в значительном количеств до высоких температур нагрева, это подтверждается экспериментально как наблюдением самих частиц, так и ограниченным ростом зерен аустинита при нагреве, вредное влияние структур сдвигового типа в сталях с феррито-перлитной структурой может быть устранено высокотемпературным отпуском.
Приведенные выше результаты, а также результаты исследования потребителей проката массового назначения подтверждают необходимость интенсивного развития производства упрочненного проката в потоке широкополосных, толстолистовых и универсальных станов. При этом прокат с пределом текучести 300-350 Н/мм2 следует получать из углеродистой стал- типа СтЗ, в основном, применяя деформационно-термическое упрощение в потоке станов.
С целью экономии легирующих элементов (в первую очередь марганца) и энергетических ресурсов, а также замены низколегированной стали упрощенной углеродистой следует проводить закалку листов с прокатного нагрева, оборудовав станы конструктивно простыми и эффективными охлаждающими устройствами, обеспечивающими заданную регулируемую скорость охлаждения. Отпуск закаленных в потоке станов листов может осуществляться в термических печах, используемых в настоящее время для нормализации. В результате появится возможность значительно увеличить производительность прокатных станов, так как для большой группы сталей отпадает необходимость в регулируемой прокатке — процесс может осуществляться при повышенных температурах с максимально возможными скоростями без ухудшения качества проката. Производство листового проката может быть дополнительно увеличено оптимальным распределением сортамента между непрерывными широкополосными и толстолистовыми станами при значительном повышении производительности последних.
Производство упрочненного в потоке станов проката из углеродистой стали взамен низколегированной равной прочности позволяет сократить расход дефицитных ферросплавов марганца до 23 кг/т прокатала также обеспечить экономию других широко используемых легирующих добавок, таких как кремний (до 7 кг/т), хром и др. Рациональное использование упрочненного в процессе деформационно-термической обработки проката из углеродистой стали позволит до 40% уменьшить расход металла (элементы конструкций, работающих на растяжение) и, как следствие, снизить энергетические, транспортные и трудовые затраты.
Деформационно-термическое упрочнение проката массового назначения
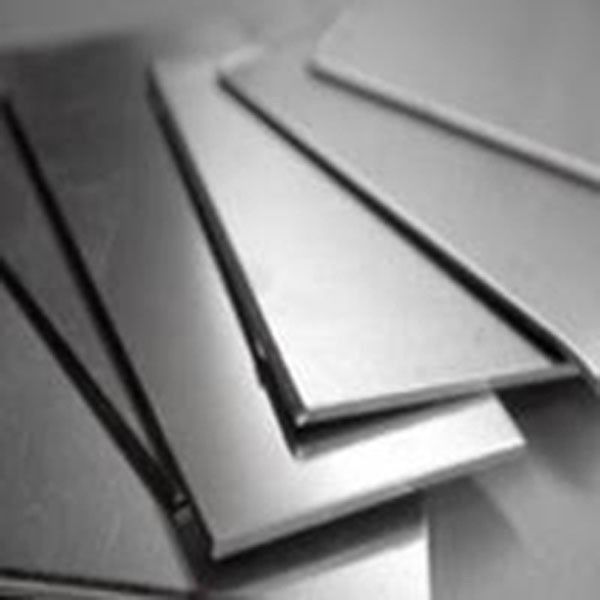
- 05/12/2013
- 3954 views
Упрочнение низкоуглеродистой стали с помощью обработок типа контролируемой прокатки оказалось эффективным на современных непрерывных широкополостных станах, например 2000, применительно к рулонным полосам толщиной 3-10 мм и шириной 1000—1800 мм.